In our modern society, flawless products are highly sought by consumers who value quality assurance. To achieve this, many companies utilize Burn-in Testing as an important method to pinpoint potential defects before they reach the hands of customers. This approach not only helps prevent early failures but also guarantees reliability and ultimately leads to satisfied customers.
This article will explore burn-in testing, covering its definition, history, benefits, challenges, and applications, highlighting its importance in ensuring high-quality products that meet consumer expectations.
The Importance of Quality Assurance in Product Development
Quality assurance (QA) ensures products meet standards before market release, building trust and credibility, and promoting customer loyalty and repeat business.
Effective QA also reduces long-term costs by identifying defects early, preventing costly recalls and repairs. Businesses must focus on QA in a competitive market to protect their reputation and enhance customer satisfaction by delivering reliable products.
Embedding quality into every stage of development—from design to production—guarantees optimal results, fosters innovation, and minimizes the risks associated with product failures.
What is Burn-in Testing?
Burn-in testing is a reliability technique in the electronics industry used to identify and eliminate early product failures. It involves exposing devices to elevated stress conditions—such as extreme temperatures, voltages, or operational loads—for a specific period. This process simulates real-world scenarios to uncover potential weaknesses that standard testing might miss.
Commonly used in industries like semiconductor manufacturing and aerospace, burn-in testing ensures that only durable products reach the market. By pushing components beyond normal limits, manufacturers can detect defects early, enhancing product quality and reliability. This thorough evaluation builds customer trust, as consumers feel more confident knowing the products they purchase have been rigorously tested.
The History and Evolution of Burn-in Testing
Burn-in testing has been a key practice in electronics since its inception, ensuring component reliability under harsh conditions before deployment. In its early days, the process involved operating devices at elevated temperatures and voltages to identify weaknesses and prevent failures after deployment, thus saving time and costs.
With technological advancements, burn-in testing methods evolved to include sophisticated software tools that simulate real-world scenarios, providing a more comprehensive understanding of product reliability. Today, burn-in testing is a standard practice in various industries, such as aerospace and consumer electronics. This evolution reflects the industry’s commitment to quality assurance and the need to meet rising customer expectations in a competitive market.
The Process of Burn-in Testing
Burn-in testing is a crucial quality assurance step that involves subjecting electronic products to extreme conditions to identify potential failures before they reach consumers. Here’s how the process typically unfolds:
- Initial Setup: The process begins by operating the device continuously under elevated stress conditions. These conditions often include increased temperatures and voltages that push the components beyond their typical operating limits.
- Monitoring and Evaluation: Throughout the test, engineers closely monitor various performance metrics. They are on the lookout for any anomalies or irregularities that might indicate weaknesses in the components or flaws in the design. This phase is critical for detecting early-life failures that could affect the product’s performance and longevity.
- Test Duration: The duration of burn-in testing varies based on product type and industry standards, ranging from a few hours to several days, depending on specific requirements and intended use.
- Post-Test Analysis: Once the testing period is complete, each device undergoes a thorough assessment. Any units that fail are carefully analyzed to determine the root cause of the failure. This analysis helps manufacturers understand and address potential issues in the design or production process.
- Quality Assurance: The burn-in testing phase ensures that only high-quality, reliable products are released to the market.
By rigorously testing products in this way, manufacturers not only enhance the reliability and durability of their offerings but also build consumer trust. The commitment to thorough testing demonstrates a dedication to quality assurance and helps maintain a strong brand reputation.
Benefits of Burn-in Testing for Companies and Consumers
Burn-in testing provides significant advantages for manufacturers and consumers, enhancing overall product quality and customer satisfaction.
- For Companies:
● Early Defect Detection: Burn-in testing detects defects early in production, preventing faulty components from reaching the market. This proactive approach reduces the risk of costly recalls and repairs, saving manufacturers time and resources.
● Quality Control: By ensuring that products can withstand rigorous conditions, burn-in testing acts as a crucial quality control measure. It helps manufacturers maintain high standards and consistency in their production processes.
● Brand Reputation: Consistently delivering reliable products enhances a company’s reputation. Investing in thorough testing can differentiate a brand in the competitive market, fostering customer loyalty and opening doors to new opportunities.
● Cost Savings: Reduced warranty claims from fewer product failures lower operational costs, leading to improved financial outcomes and better resource allocation for businesses over time.
- For Consumers:
● Enhanced Reliability: Products that undergo burn-in testing are more reliable and durable, giving consumers confidence in their purchases. Knowing that a product has been thoroughly tested for performance and longevity provides peace of mind.
● Higher Satisfaction: When products perform as expected and last longer, customer satisfaction increases. This not only reduces the likelihood of returns but also enhances the overall customer experience.
● Safety Assurance: Especially in critical industries like aerospace and medical devices, burn-in testing ensures that products meet safety standards, which is crucial for protecting consumers and preventing accidents.
Overall, burn-in testing is a valuable practice that benefits both companies and consumers. It helps manufacturers produce high-quality, reliable products while giving consumers confidence in their purchases, leading to a win-win scenario.
Challenges and Limitations of Burn-in Testing
Burn-in testing, while valuable for quality assurance, comes with several challenges and limitations that manufacturers must navigate.
- Resource Intensive: Burn-in testing involves substantial investment in specialized equipment and facilities and can be time-consuming, increasing operational costs. These expenses can be challenging for smaller companies, affecting their ability to compete with larger firms.
- Misleading Failure Rates: High failure rates during burn-in can be difficult to interpret. While they may indicate issues with the product, they can also create confusion about its overall reliability. Distinguishing between genuine product flaws and normal early-life failures can be challenging, complicating production and quality assurance decisions.
- Focus on Early Failures: Burn-in testing is primarily designed to identify early-life failures, often referred to as “infant mortality” in components. However, it does not fully account for long-term performance or potential issues that could arise under different conditions over time. This limitation means that while burn-in testing improves initial reliability, it doesn’t guarantee longevity.
- Real-World Simulation Challenges: Recreating real-world operating conditions in a controlled testing environment can be difficult. Variations in temperature, voltage, and other stress factors can lead to inconsistent data. As a result, the effectiveness of burn-in testing in predicting actual product performance in diverse, real-world environments may be limited.
- Efficiency vs. Accuracy: Striking the right balance between thoroughness and efficiency in burn-in testing is a significant challenge. While more extensive testing can lead to better insights, it also increases costs and time. On the other hand, shorter, less rigorous tests may miss critical issues, leading to potential reliability problems after the product reaches the market.
These challenges underscore the importance of carefully planning and executing burn-in testing processes to maximize their benefits while managing the inherent limitations.
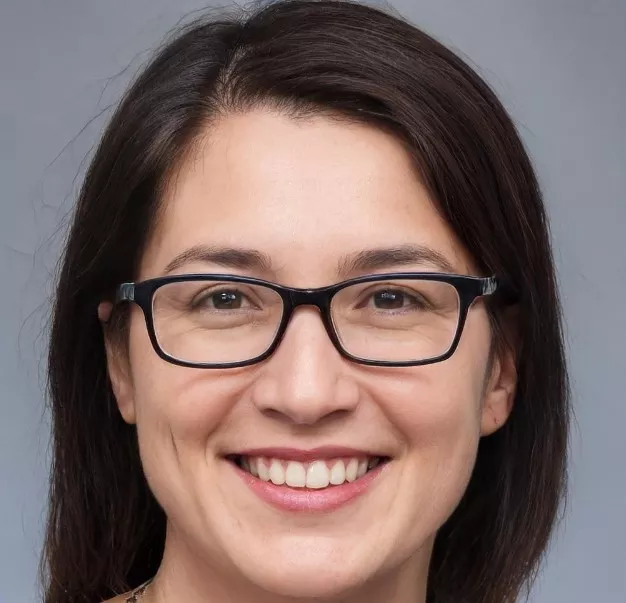
Aretha Davis, the wordsmith extraordinaire, weaves enchanting tales with her pen and keyboard. A renowned blogger and writer, her captivating prose transports readers to realms unknown. Join her literary journey and be swept away by the magic of her words.