Lockout tagout stations have been commonplace in factories and industrial settings for years. The goal is to de-energize and secure large workplace equipment and machinery so that the hazardous energy isn’t introduced again during repair or servicing procedures.
One of the most common tools to aid the process is a lockout tagout station. It is a simple thing that can feel complicated without proper guidance. Read on to find out more about lockout tagout stations and how they can be so beneficial in the workplace.
Lockout Tagout History
In order to get a better understanding of how lockout stations, lock out tags, and similar safety equipment in the business works, it helps to have a brief history. OSHA implemented standards around 1982 regarding the lockout tagout program. It didn’t go into effect legally until 1989 but has been a standard for workplace safety.
It is estimated that lockout tagout stations save as many as 120 lives each year and prevent more than 50,000 injuries. They play a vital role in workplace safety and are easy to implement, which is why they are so commonly found. OSHA even provides tips and a litany of resources as it pertains to safety and requirements for lockout tagout stations.
What is the Difference Between Lockout and Tagout?
Though the name includes the two, there is a distinct difference between “lockout” and “tagout.” Here is what to know about each of them and how they play a vital role in the safety of workers.
Lockout
The lockout process is when any kind of electrical source – hydraulic, pneumatic, mechanical, electrical, thermal, chemical, or other – is physically isolated from the rest of the system that uses it. Generally, that is a singular piece of equipment or machinery using lockout devices and padlocks that are used for the specific application. Circuit breaker or valve lockouts are used for very specific lockout jobs.
Tagout
The tagout process, however, involves a simple tag or label. The goal in using these is that it communicates essential information about what is happening with that piece of equipment or machinery. It also illustrates why it is so important.
Some of the details on a tag include a warning or danger sign, specific instructions (typically “do not operate”), the purpose, timing, and the name of the person. Tagout on its own is not ideal, but when combined with lockout procedures, it can be quite the safety tool.
Lockout Tagout Best Practices
Part of what makes the lockout tagout process so effective is adhering to best practices. Keeping up with them will ensure that employees remain educated on safety protocols and the best way to perform maintenance or repairs on specific machinery.
One thing about lockout tagout stations is that they must be inspected periodically. There should not be years between inspections because then there is no telling whether the lockout devices are still effective. Generally speaking, an annual review of all procedures and devices is an ideal solution.
Other best practices include things like lockout tagout software, program standardization, having updated isolation points, authorized annual training, contractor training, and device inventory.
Remaining Compliant
It is also important to ensure that the business remains compliant when it comes to OSHA standards regarding lockout tagout stations. To be OSHA-compliant, there are three things that must be included.
Task-specific procedures must be in place so that workers are aware of safety protocols in those specific situations, not in some general sense. Workplace regulations must also be clearly posted and visible. Finally, lockout tagout stands, like updating and maintaining equipment lists, are necessary for any station.
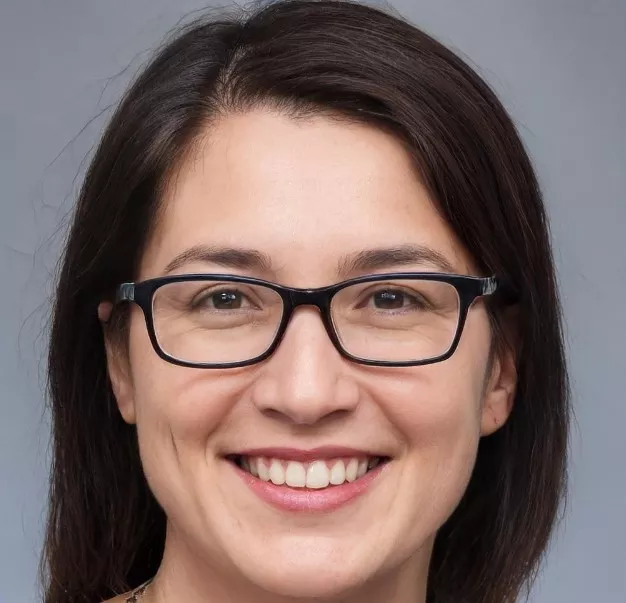
Aretha Davis, the wordsmith extraordinaire, weaves enchanting tales with her pen and keyboard. A renowned blogger and writer, her captivating prose transports readers to realms unknown. Join her literary journey and be swept away by the magic of her words.